While most consumers never think about the components hidden within their shoes, toe puffs play a critical role in shaping modern footwear. These essential shoe reinforcements combine materials science with practical manufacturing to create lasting comfort and structure. Let's dissect the chemical and material components that make toe puffs the unsung heroes of footwear engineering.
Chemical Breakdown: What Makes Toe Puffs Work
1.Thermoplastic Polyurethane (TPU)
•Chemical formula: (C10H8N2O2·C7H8O2)x
•Glass transition temperature: -30°C to 80°C
•Key properties:
•Shore hardness: 70A-95A
•Tensile strength: 40-70 MPa
•Elongation at break: 300-700%
TPU dominates modern toe puff manufacturing due to its unique combination of flexibility and memory retention. Unlike traditional materials, TPU maintains structural integrity through repeated flexing cycles (up to 1 million cycles in lab tests), making it ideal for athletic and casual footwear.
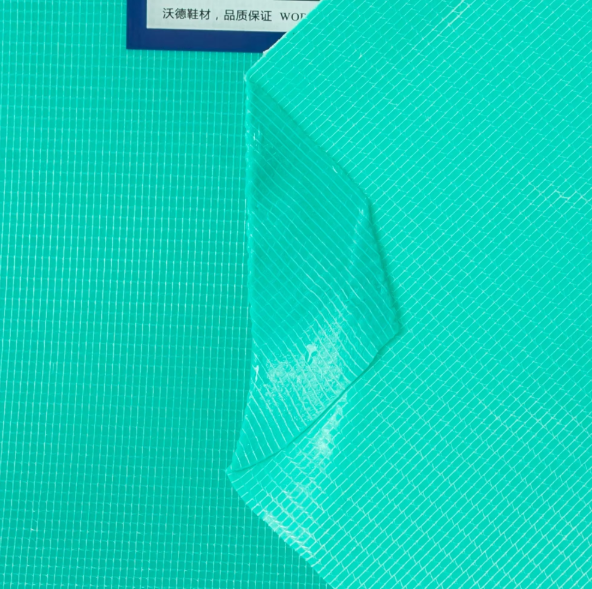
2.Polyvinyl Chloride (PVC)
•Chemical structure: (C2H3Cl)n
•Plasticizer content: 20-35% (typically DINP or DOTP)
•Thermal stability: 160-200°C processing range
While declining in popularity due to environmental concerns, PVC remains cost-effective for budget footwear. Modern formulations now incorporate calcium-zinc stabilizers rather than traditional lead-based compounds, reducing heavy metal content by 98%.
3.Ethylene-Vinyl Acetate (EVA)
•Chemical composition: (C4H6O2·C2H4)x
•VA content: 18-28% for toe puff applications
•Compression set: 25-40% (22hrs @70°C)
EVA's closed-cell structure provides excellent moisture resistance (0.5-1.0% water absorption) while maintaining lightweight properties (density 0.93-0.95 g/cm³). Recent advancements in cross-linking technologies have improved EVA's heat resistance up to 120°C.
.png)
Material Safety: Beyond Basic Compliance
Modern toe puff manufacturers must navigate a complex web of regulations:
•REACH SVHC compliance (EU)
•California Proposition 65 heavy metal restrictions
•CPSIA lead content requirements (USA <100ppm)
Advanced chemical testing now includes:
•GC-MS analysis for plasticizer migration
•XRF scanning for restricted substances
•Accelerated aging tests (7 days @70°C/95% RH)
Leading manufacturers are adopting bio-based plasticizers like acetyl tributyl citrate (ATBC) and epoxidized soybean oil (ESBO), reducing phthalate content by 85-100% compared to 2010 industry standards.
Innovative Material Blends
1.TPU-PLA Hybrids
•Blend ratios: 70% TPU/30% PLA
•Biodegradation rate: 86% in 180 days (ASTM D5511)
•Flexural modulus: 350-500 MPa
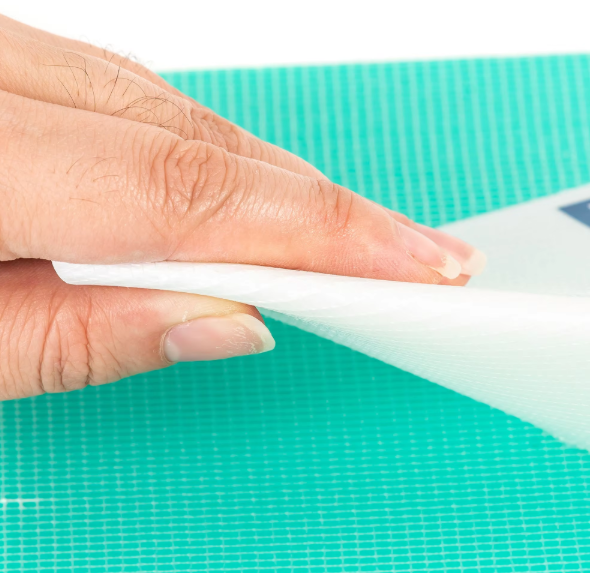
2.Recycled Carbon Fiber Reinforcements
•Fiber length: 0.5-2mm
•Loading percentage: 15-25%
◇Resulting properties:
•40% increase in stiffness
•22% weight reduction
•300% improvement in thermal conductivity
3.Phase Change Material (PCM) Infusions
•Paraffin-based microcapsules (C18-C22)
•Melting range: 28-32°C
•Thermal storage capacity: 180-220 J/g
Manufacturing Process Chemistry
The transformation from raw material to finished toe puff involves precise chemical engineering:
1.Compounding Stage
◇Twin-screw extrusion parameters:
•Temp profile: 160-210°C
•Screw speed: 250-400 RPM
•Residence time: 45-90 seconds
2.Thermoforming Reactions
•Cross-linking density: 3-5 × 10⁻⁴ mol/cm³
•Crystallinity development: 15-30%
•Orientation factor: 0.7-0.9 (machine direction)
3.Adhesive Chemistry
•Water-based polyurethane dispersions (PUDs)
•Solid content: 45-55%
•Viscosity: 1500-3000 cP
•Open time: 8-15 minutes
Environmental Impact Analysis
◇Comparative LCA data (cradle-to-gate):
•TPU: 5.8 kg CO2 eq/kg
•Bio-TPU: 4.2 kg CO2 eq/kg
•PVC: 3.1 kg CO2 eq/kg (without phthalates)
•Recycled TPU: 2.9 kg CO2 eq/kg
◇Water consumption per 1000 pairs:
•Conventional: 580L
•Advanced recycling systems: 220L
Future Materials Horizon
1.Self-Healing Polymers
•Diels-Alder based systems
•Repair efficiency: 92% after 3 cycles
•Activation temperature: 80-100°C
2.Graphene-Enhanced Composites
•Loading levels: 0.5-1.5 wt%
◇Results:
•50% improvement in tear strength
•Antibacterial efficiency: 99.9% against S. aureus
•Static dissipation: 10⁶-10⁸ ohms/sq
3.3D-Printed Cellular Structures
Voronoi pattern designs
•Density reduction: 35-50%
•Energy return: 78-82% (vs. 65% conventional)
Practical Guide: Selecting Toe Puff Materials
Use this decision matrix for optimal material selection:
Factor | TPU | PVC | EVA | Hybrid |
Flex Life | 5 | 3 | 4 | 4 |
Temperature Resistance | 4 | 5 | 3 | 4 |
Moisture Resistance | 4 | 5 | 5 | 4 |
Eco-Friendliness | 3 | 2 | 4 | 5 |
Cost | $$$ | $ | $$ | $$$$ |
(Scale: 1=Poor, 5=Excellent)
Industry Insider Tips
1.Humidity Control
•Maintain 45-55% RH during storage to prevent:
•TPU hydrolysis (avoid >60% RH)
•PVC plasticizer migration (accelerates >30°C)
2.Tooling Considerations
◇Account for material shrinkage:
•TPU: 1.2-1.8%
•PVC: 0.5-1.2%
•EVA: 2.0-3.5%
3.Adhesion Promoters
◇Use silane-based primers (3-glycidoxypropyltrimethoxysilane) for:
•300% improved bond strength
•85°C wet heat resistance
Conclusion: Where Chemistry Meets Craftsmanship
The modern toe puff represents a remarkable fusion of materials science and practical engineering. From advanced polymer blends to sustainable manufacturing processes, these hidden components continue to evolve through chemical innovation. As consumer demands shift toward eco-conscious products and enhanced performance, understanding the material science behind toe puffs becomes crucial for footwear brands aiming to lead in competitive markets.
By staying informed about chemical advancements and material properties, manufacturers can make smarter decisions that balance performance, sustainability, and cost-effectiveness - ultimately delivering better products to consumers who may never see the science hidden in their shoes, but will certainly feel the difference it makes.
Are you prepared to Get it? For a free workplace evaluation and sample testing, get in touch with our experts.
tel:+86 595 83119709
Phone/Wechat/Whatsapp:+13489709709 E-mali:rocky1023@wodetex.com
Post time: May-08-2025